Research, Development & Innovation (RD&I)
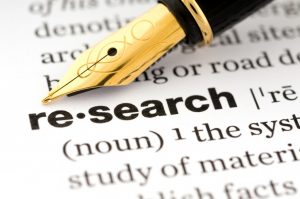
RDI Mission
- Continuous improvement of the technical capability and reliability of the NDE and material testing services provided by the company;
- Contributions to the National and European research projects in our field of activity.
RD&I Management
The RD&I activities are performed in the framework of definite projects, with financial support ensured by our company and / or by National & European research projects;
The RD&I Programs are initiated by the top management of the company.
The Director of the company is, also, the RD&I Manager, being in charge to evaluate the progress on each established program, and to request implementation of corrective actions, when necessary.
The most qualified personnel of the company are involved in the RD&I activity, in parallel with their current activity.
However, the Development and Innovation Center (CDI) play an essential function in the framework of RD&I, this department being specialised in design and execution of the systems, equipment and devices which are necessary or are the results of RD&I. The CDI department has highly experienced personnel in mechanical, electric, electronic and software design and execution.
Significant national & international RD&I Projects
International RI&D Projects:
-
- CRP I3.30.10 coordinated by International Atomic Energy Agency – Vienna (Intercomparison of the NDE methods for CANDU fuel channels inspection and diagnosis);
CORFAT_FP7- GA 218637 / 2008: European R&D Program (development of cost effective corrosion and fatigue monitoring systems for transport products);
National RI&D Projects:
- CAFICMEIS (evaluation and implementation of inspection methods for composite materials);
- SINERMAT (development of non-invasive examination methods for advanced materials);
Significant internal RD&I Projects
Internal RDI Projects of NNDT:
- Design, execution and qualification of the DC permeameter NNDT-DCMP-01 for characterization of magnetic properties of steel;
- Design, execution and qualification of the machines NNDT-TT-01, NNDT-TT-02, NNDT-TT-03 for Post Weld Heat Treatment;
- Design, execution and qualification of the Digital Borescope NNDT-DBVT-01 for visual examination of inside bore of the large forged rotors;
- Design, execution and qualification of the Digital Microscope NNDT-FDM-01 for direct in – situ metallographic examinations;
- Development of Spectral Ultrasonic Imaging techniques for assessment of signals obtained during UT examination of large forged components in order to discriminate between ultrasonic indications from cracks, hydrogen flakes, non-metallic inclusions, alloying element segregations or other discontinuities;
- Development of Automatic Ultrasonic Imaging systems for boresonic examination of the large forged rotors;
- Development of Automatic Ultrasonic Imaging systems for peripheral inspection of the large forged rotors;
- Design, execution and qualification of high effieciency Wave Guides for Acoustic Emission Testing at elevated temperature;
- Elaboration and validation of methodologies for technical inspection of pressure equipments based on high temperature NDE techniques for investigation of the structural integrity during operation;
- Design, execution and qualification of the Advanced Ultrasonic Beckscattering Testing system for detection and caracterization of the High Temperature Hydrogen Attack (HTHA) in steel pressure equipment;
- Elaboration of investigation methodologies, numerical models and written procedures for evaluation of remaining life of pressure equipments subjected to various degradation mechanisms (corrosion / erosion, fatigue, creep, etc.)
- Of a special importance is the TREND project related to development of techniques and procedures for Non – Destructive Examinations at High Temperatures. In the framework of this program, various NDE methods were already extended to higher temperatures, and accepted by the regulatory body to be applied for pressure equipment, during plant operation:
- Ultrasonic Testing (UT-HT), including Phased Array (PAUT-HT), up to 300 °C
- Liquid penetrant examinations (PT-HT): up to 200 °C
- Magnetic particle examinations (MT-HT): up to 427 °C
- Ultrasonic determination of thickness (UTg-HT): up to 540 °C
- Acoustic Emission examination of pressure equipment: no temperature limit during operation because of the high acoustic wave guides developed in our company